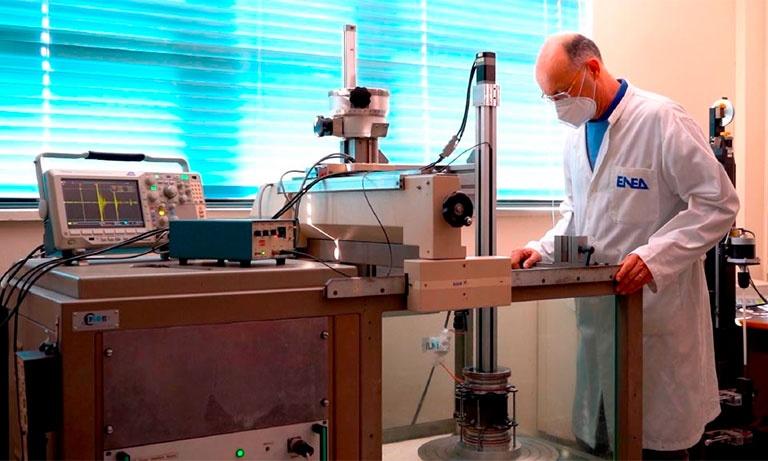
I sistemi di mappatura non distruttiva UT
DOI 10.12910/EAI2021-099
di Angelo Tati, Laboratorio Materiali e processi chimico-fisici - ENEA
Per le attività di ricerca sui nuovi materiali e componenti utilizzati in campo nucleare ed aerospaziale, l’ENEA ha sviluppato un software di acquisizione ed elaborazione per controlli non distruttivi (non destructive testing) e, in particolare, per la tecnica ultrasonora. I risultati ottenuti stati presentati a vari congressi nazionali, attirando l'attenzione delle ditte operanti nel settore dei controlli non distruttivi, in particolare del comparto aeronautico.
Per le attività di ricerca sui nuovi materiali e componenti utilizzati in campo nucleare ed aerospaziale, l’ENEA ha sviluppato un software di acquisizione ed elaborazione per controlli non distruttivi (non destructive testing) e, in particolare, per la tecnica ultrasonora[1]. I metodi applicati sono quelli degli esami clinici, quali la radiografia, gli ultrasuoni e diversi altri, più specifici, in grado di garantire l’assenza di difetti che ne compromettano il funzionamento, e allo stesso tempo non “invadano” o distruggano l’oggetto esaminato. Il software gestisce, tramite computer e schede elettroniche, dei sistemi motorizzati ed acquisisce i segnali provenienti dai sensori relativi al metodo utilizzato. I dati ottenuti sono elaborati per ottenere delle mappature in bianco e nero e falsi colori che evidenziano i difetti presenti nel materiale.
Tutti i metodi si avvalgono di sistemi automatici che aiutano l’esperto a valutare la ‘salute’ del componente in modo veloce e ripetibile sollevandolo da un compito certe volte lungo e stancante. L’esame ultrasonoro è un metodo molto efficace se abbinato ad un sistema d’ispezione motorizzato.
Gli ultrasuoni
Come per tutti i fenomeni ondulatori, è possibile definire per le onde sonore una lunghezza d’onda, un periodo T e una frequenza f, grandezze che sono legate fra loro dalle relazioni della meccanica ondulatoria, mentre c rappresenta la velocità di propagazione del suono nel mezzo considerato. Tuttavia, a differenza della luce, le onde acustiche necessitano per la loro propagazione, di un mezzo elastico nel quale viaggiare. Ciò spiega perché nel vuoto non si propaga alcun suono. Quando la frequenza di tale onda sonora è compresa nel range tra 20 e 20000 Hz si parla di suoni udibili, mentre laddove il valore di 20 KHz sia oltrepassato si parla di ultrasuoni.
Sviluppo del software di mappatura ultrasonora
Lo sviluppo di un software di mappatura ultrasonora ha avuto inizio negli anni 80 con l'acquisto di una macchina a 3 assi cartesiani motorizzati e 2 assi rotativi manuali per l'orientazione della sonda ad ultrasuoni. L'acquisto fu realizzato dal laboratorio di Controlli non Distruttivi dell'ENEA Casaccia il cui responsabile era il collega Ing. Franco Imperiali. Questa macchina sviluppata dalla ditta Gilardoni era nata per lo sviluppo e la caratterizzazione delle sonde ad ultrasuoni ed era utilizzata dall'ENEA per la messa a punto di tecniche ultrasonore in campo nucleare e controllo di componenti di grosso spessore. Una seconda macchina, più grande della prima, fu sviluppata a partire dagli 90 dalla ditta Contek in collaborazione con l'ENEA Frascati per controllare componenti di grandi dimensioni e geometria complessa. La macchina fu dotata di un braccio portasonda con due assi rotativi motorizzati in grado di muovere la sonda e inseguire la superficie dei pezzi curvi [2].
Agli inizi degli anni ‘90 l’acquisto dei primi personal computer nei laboratori dell'ENEA permise di utilizzare delle schede di interfaccia hardware per la comunicazione con gli oscilloscopi, per l'acquisizione dei segnali ultrasonori, e con le macchine di movimentazione automatica suddette. La connessione di questa strumentazione al computer e l'uso di ambienti di sviluppo software a partire dal pacchetto ASYST e successivamente con il linguaggio Basic, C ed ASSEMBLER permisero la creazioni delle prime applicazioni automatiche ad ultrasuoni.
La difficoltà iniziale di questi software fu la gestione di grandi quantità di dati, la durata molto lunga delle misure e la presentazione grafica dei risultati che fu risolta nel corso dei 10 anni successivi con la comparsa di computer più potenti dotati di processori multi-thread, schede video con memoria dedicata, RAM di decine di Megabyte e dischi con spazio di memorizzazione di alcune decine di GigaByte.
Negli anni 2000 appare sul mercato l'ambiente di sviluppo Labview che permette di realizzare applicazioni grafiche in modo veloce avendo a corredo diverse librerie (grafica, comunicazione, acquisizione, controllo motori, visione e elaborazione segnali, ecc.). Il vantaggio di questo ambiente di sviluppo è la programmazione tramite icone grafiche e fili di connessioni simili ad un circuito elettrico che permette un rapido sviluppo rispetto ai linguaggi tradizionali supportati da testo e compilatore. La società National Instruments (NI) sviluppatrice del LABVIEW ha inoltre sviluppato delle schede hardware di acquisizione segnali e immagini, controllo motori che integrati insieme al software permettono la creazione di applicazioni molto complesse.
Applicazioni in campo aerospaziale
Il primo progetto in campo aerospaziale che ha visto l'utilizzo del software di mappatura ad ultrasuoni (Software UT) è stato per il controllo di un disco di turbina in titanio con un anima interna in fibra di carbonio prodotto dalla società AVIO. Questa collaborazione ha permesso poi di realizzare il progetto Europeo AWFORS (Advanced Welding Technologies For Repair and Salvage of high valued engine components on nickel and titanium based alloys) del Quinto Programma Quadro UE (1998-2002) insieme al CSM ed altri pattern europei fra cui il Fraunhofer Tedesco. Il progetto puntava a realizzare un disco di turbina con palette integrate partendo da un unico blocco di metallo opportunamente lavorato di macchina ad asporto di truciolo e senza la calettatura di palette separate. Inoltre prevedeva la messa a punto di diversi metodi di riparazione/saldatura delle palette tra cui il laser cladding e la saldatura con scarica capacitiva.
La macchina di mappatura ultrasonora è stata utilizzata per il controllo non distruttivo delle barrette a trazione in leghe metalliche di diverso tipo tra cui l'inconel, il titanio, il renè e l'acciaio. Le barrette erano prima divise in due parti, poi saldate tra di loro con i vari metodi e poi sottoposte ai test non distruttivi ed infine ai test meccanici. I controlli non distrutti delle barrette cilindriche sono stati condotti tramite il Software UT utilizzando due assi motorizzati per la scansione. L'asse Z alzava e abbassava la barretta, l'asse rotativo girava la barretta di 360° e la combinazione dei due movimenti permetteva alla sonda fissa su un lato, di scandire l'intera superficie controllandone il volume interno. Analogo software fu realizzato per il metodo a correnti parassite o Eddy Current.
Il progetto prevedeva la produzione anche di barrette a profilo alare saldate similmente a quelle cilindriche. In questo caso il software UT a 2 assi non fu sufficiente per il controllo non distruttivo, perciò è stato sviluppato un nuovo software a 4 assi motorizzati. La forma alare delle barrette rendeva problematica la loro rotazione rispetto alla sonda fissa perciò l'unica alternativa praticabile era far muovere la sonda intorno al campione fissato ad un supporto.
La soluzione fu estrarre il profilo della superficie della barretta, da un file CAD di tipo STL (Stereo Lithography interface format), lo stesso file con cui era realizzata meccanicamente tramite le macchine a controllo numerico (CNC). Il file STL consiste in una mesh di piccoli triangoli che descrive la superficie esterna del pezzo; questa viene processata da un programma sviluppato ad hoc estraendo i triangoli relativi ad una determinata quota Z (zona da controllare). I triangoli sono rappresentati dalle coordinate dei 3 vertici e dai 3 coseni direttori che ne determinano l'orientazione nello spazio.
Queste informazioni estratte ed opportunamente elaborate vengono poi utilizzate dal software di mappatura per muovere la sonda UT intorno al campione secondo una traiettoria composta dalle coordinate : X , Y e l'angolo della sonda. Questo movimento ha permesso alla sonda di ruotare intorno alla barretta ed essere sempre perpendicolare alla superficie. Il software fu sviluppato per controllare il provino sia con gli ultrasuoni e con l'Eddy Current (EC) mostrando su unica interfaccia grafica i risultati di entrambe le tecniche. Il software passava da un movimento a 2 gradi liberta a 4 gradi libertà e questa traguardo permise nuove applicazioni sempre più complesse.
Questi risultati sono stati esposti a vari congressi nazionali, attirando l'attenzione delle ditte operanti nel settore dei controlli non distruttivi, in particolare del settore aeronautico.
La prima applicazione del software all'esterno
La prima applicazione del software all'esterno dell'ENEA fu il controllo di una pala del rotore secondario dell'elicottero A109 dell'Agusta/Westland. Il componente da analizzare, in materiale composito in vetro e carbonio, assicurava la pala al mozzo del rotore. Nelle precedenti applicazioni veniva impiegata la tecnica in riflessione o ecografica (Pulse-Echo,PE) ed una sonda unica, mentre in questo caso la tecnica utilizzata si chiama "in trasmissione" (True Trasmission, TT) e sfrutta due sonde UT; se il campione da controllare è chiuso si trova tra le due sonde, mentre se presenta una cavità troveremo una sonda esterna o una interna allo stesso. I materiali compositi a differenza di quelli metallici hanno una forte attenuazione dell'onda sonora. Il pezzo da controllare è immerso in acqua per assicurare la trasmissione dell'onda ultrasonora; quest'ultima partendo dalla sonda interna attraversa lo spessore del cilindro giunge alla sonda esterna. L'intensità dell'onda, convertita in un segnale elettrico, determina la qualità del materiale attraversato composto da vari strati di matrice polimerica e da fibre di rinforzo in vetro o carbonio. Il movimento della pala secondo l'asse Z e la sua rotazione permette di controllare lo spessore del cilindro per la sua lunghezza ricostruendo così una mappa in falsi colori. La mappa rappresenta lo sviluppo circonferenziale del pezzo. Il difetto viene rappresentato sulla mappa da una zona rossa indicante,per esempio, una delaminazione (disbonding) di qualche strato del composito.
L'ENEA partecipò al progetto fornendo il software di mappatura, la consulenza alle prove sui campioni con difetti artificiali e naturali e al collaudo finale della macchina. Il capo commessa fu la ditta del settore CND che ha fornito lo strumento UT, l'oscilloscopio, le sonde. La macchina a 2 assi fu realizzata da ditta di meccanica di precisione ed infine la parte elettrica ed elettronica comprensiva di PLC e joystick a schermo LCD fu realizzata da una ditta di elettronica.
A questo progetto ne seguì un altro più complesso, con l'intento di fornire un sistema che unisse le due tecniche TT e PE per controllare le pale e il mozzo del rotore principale dell'elicottero EH101 (Agusta/Westland). Le pale lunghe 9 metri e il rotore largo più di 2 metri richiesero la realizzazione di una macchina larga 2,5 m, lunga 4 m e alta 2,5 m. In questo caso le pale in composito venivano controllate dividendo in settori la lunghezza. La tecnica utilizzata era la TT e le sonde erano inserite ognuna all'interno di un supporto in plexiglass generanti una colonna d'acqua (Squirter) per l'impossibilità di immergere l'intero pezzo in acqua. La colonna d'acqua è generata da un ugello e da una pompa elettrica che spinge l'acqua all'interno dello squirter; l'acqua della colonna colpisce il pezzo creando una particolare forma ad ombrello priva di turbolenze, l'acqua utilizzata viene raccolta da una vasca sottostante e rimessa nel ciclo. Il mozzo è stato controllato con la tecnica PE sempre tramite un singolo Squirter. Il mozzo in composito e titanio presentava una pianta pentagonale con 5 fori interni uno per ogni lato. In questi fori venivano poi fissate le pale nella fase finale dell'assemblaggio dell'elicottero.
Il mozzo con profili curvi fu controllato da un software simile a quello sviluppato per il progetto AWFORS con la differenza che la paletta aveva una larghezza di circa 2 cm mentre il mozzo un diametro di più di 2 metri.
Il progetto successivo in collaborazione nuovamente con AVIO fu il progetto FANTASIA (Flexible and Near-net-shape generative manufacturing chains and repair techniques for complex shaped aero engine parts) nel quale l'ENEA mise in atto una campagna di controlli non distruttivi con 5 tecniche diverse:
- Esami Visivi-VT
- Eddy current-ET
- Liquidi penetranti fluorescenti-PT
- Raggi X-RT
- Ultrasuoni-UT
Per la messa a punto delle tecniche non distruttive sono stati progettati e costruiti campioni di riferimento con geometrie diverse e aventi all'interno difetti artificiali. Il materiale esaminato era una lega di titanio con cui sono fatte le palette di turbina degli aerei moderni capaci di resistere ad altissime temperature e dotati di un peso specifico basso (4 507 kg/m³). Il risultato fu che le prime tre tecniche permisero una ispezione veloce in grado di rilevare difetti molto piccoli sia superficiali che sub-superficiali ma senza determinare le dimensioni dei difetti. Mentre le ultime due tecniche determinarono le dimensioni del difetto nelle tre dimensioni e che per questo vengono chiamate tecniche volumetriche. Gli UT e RT necessitano del supporto del computer per l'elaborazione delle immagini. Per queste ragioni le prime tre tecniche furono utilizzate per l'esame non distruttivo di grandi fogli di lamiera in titanio prodotte tramite laminatura e servirono per delimitare le zone prive di difetti dove estrarre i campioni per le successive lavorazioni. Mentre le tecniche volumetriche furono utilizzate per l'esame dei campioni prima e dopo le saldature laser.
Seguirono a queste attività di laboratorio lo sviluppo di una macchina ad ultrasuoni per il controllo del radome in materiale ceramico. Trattasi di quel componente aeronautico che contiene il RADAR e che deve essere trasparante alla radiazione elettromagnetica emessa. La macchina e il software di mappatura hanno permesso di controllare l'incollaggio del materiale ceramico ad un anello di lega INVAR.
Le esperienze scaturite da questi progetti sopra brevemente descritti, sono in realtà risultati fondamentali per la messa appunto dei software di analisi dei dati ultrasonori (BigDATA). Il software di mappatura fu utilizzato nel Progetto ELIOS (Progettazione di componenti aeronautici in titanio saldati con impianto laser in fibra) per la verifica delle saldature in titanio di spessore di circa 3 millimetri tramite una tecnica definita TOFD (Time of Difraction) che permette l'analisi della giunzione saldate testa-testa con una singola scansione lungo la saldatura. I risultati vengono esposti al convegno delle prove non distruttive nella sessione AEROSPAZIO tenuto nel 2015 a Milano. Con l'Università UNICUSANO di Roma e la collaborazione del Professor Tiziano Pagliaroli vengono svolte due tesi riguardanti il comportamento di una superficie alare trattata con lavorazioni di microforatura in un regime supersonico. Per questo tipo di controllo vengono utilizzate due sonde ad ultrasuoni con accoppiamento in aria che simulano l'impatto dell'aria sul campione microforato; l'onda generata dalla sonda viaggia alla velocità del suono in aria pari a 340 m/s corrispondente a 1 235 Km/h corrispondente a Mach 1.
Sviluppo del software di mappatura per motori criogenici aerospaziali
Nel 2017 l'ENEA viene contattata da una società che fornisce servizi ad AVIO SPAZIO per la messa a punto di saldo-brasature da utilizzare per la costruzione di camere di combustione per motori criogenici. Dopo il controllo ultrasonoro di un provino piano che simula una piccola porzione della camera cilindrica, si dimostra come la tecnica di mappatura ultrasonora evidenzia la qualità della saldatura. Si avvia così una collaborazione che vede il controllo UT di un primo prototipo in scala ridotta di una camera di combustione in rame ed Inconel [3] saldo-brasate.
La camera è composta da una parte cilindrica, una convergente e una divergente entrambi con un profilo tronco-conico. Per questo tipo di controllo si sviluppa un software dove la sonda segue il profilo della superficie tramite 2 assi motorizzati X e Z mentre la camera ruota su una tavola rotante. La camera è appoggiata sulla tavola tramite un strato di gomma che funge da guarnizione. La camera in questo modo può contenere l'acqua e la sonda, permettendo così il controllo UT. La tecnica si rivela vincente per una successiva serie di camere prodotte con la tecnica ALM (Additive Layer Manufacturing).
[1] I controlli non distruttivi sono gli esami che si eseguono sui materiali e sui componenti costituenti un qualsiasi manufatto per garantire, in termini di affidabilità sia strutturale che prestazionale, l’efficace comportamento del componente stesso.
[2] Le macchine sono sempre corredate da una grossa vasca per contenere il pezzo che è immerso in acqua per l'accoppiamento sonda-pezzo.
[3] Inconel è un marchio registrato dell'azienda statunitense Special Metals Corporation e fa riferimento alla famiglia delle superleghe a struttura austenitica a base di nichel-cromo